This chapter addresses the specific tasks by industry to prepare onsite emergency planning and establish cooperation for offsite planning.
OECD Guiding Principles for Chemical Accident Prevention, Preparedness and Response - Third Edition
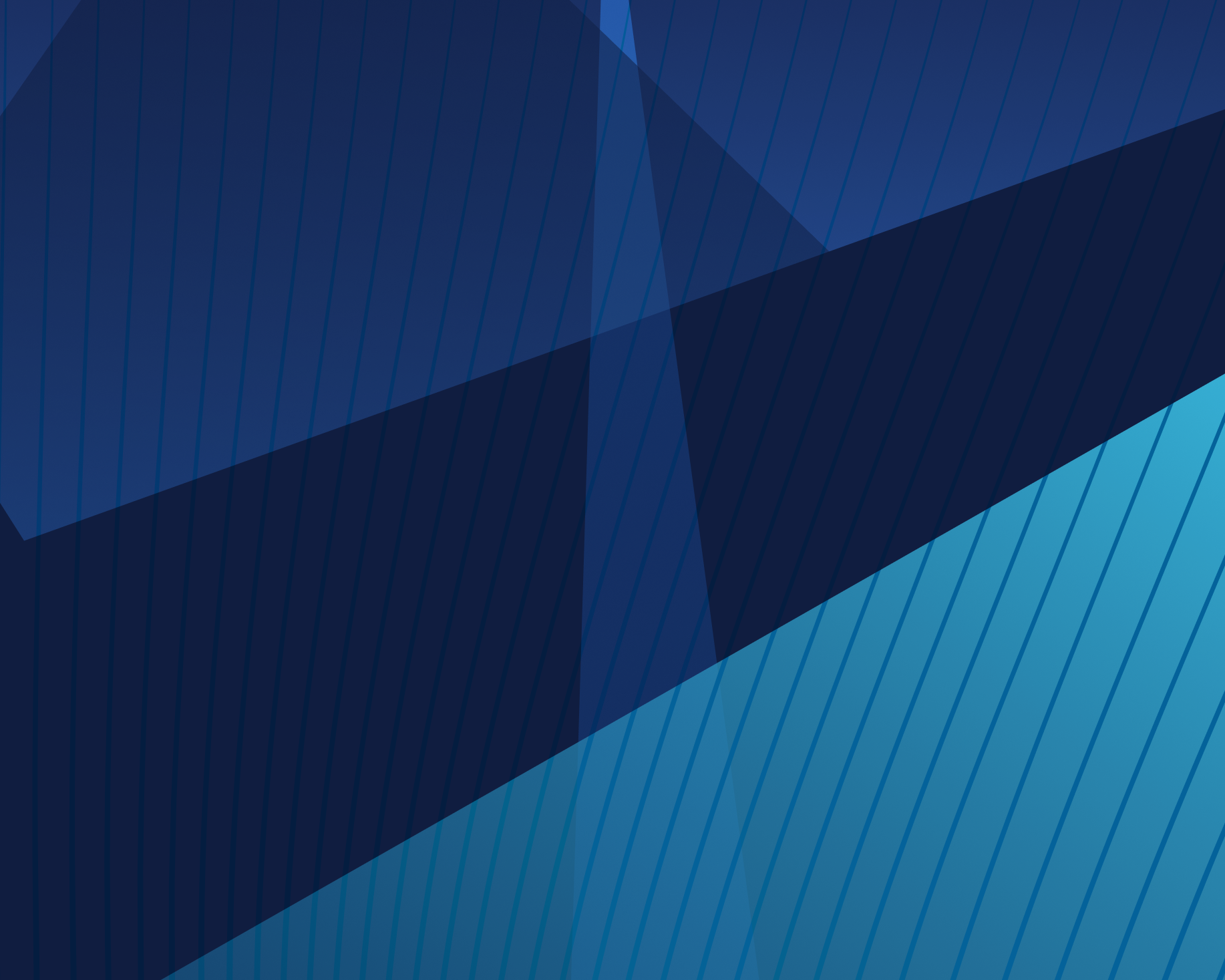
5. Emergency preparedness and mitigation: Principles to industry
Abstract
Develop an onsite emergency plan
All facilities should have a suitable onsite emergency plan, which covers all installations of that facility and is based on a complete range of accident scenarios, including most probable chemical accidents as well as scenarios with lower probability but high consequences.
Management of all hazardous installations – including enterprises that are not considered part of the chemical industry but use or handle hazardous substances – should identify and assess the full range of accidents that could arise at the installations as well as the appropriate response actions. This information should be available in safety reports or related reports, where such reports have been prepared (see section on risk assessment and safety reports in chapter 2).
An onsite emergency plan should contain:
A scale plan of the site.
A list of all hazardous substances handled, indicating the quantities involved, and their locations on the site.
A description of the hazards involved, including information regarding each hazardous substance and the conditions under which it is processed, handled and stored.
First aid needs in the event employees or the public are exposed to a hazardous substance.
A description of the surrounding area and a description of the relevant population.
Onsite emergency plans should also provide for the emergency shutdown or bringing to, and keeping in, a safe state of operation. Procedures for doing this must be defined in the safety management system (see section on safety management system in chapter 2).
Emergency plans should contain clear criteria that establish when public authorities should be called in to respond to accidents with potential offsite effects.
These criteria should make it clear at what stage to contact public authorities, and whom to contact.
The fact that public authorities are involved in response does not change the fact that the enterprise remains responsible for the safety of its installations, including the adverse effects of any accidents.
Onsite emergency plans should identify the roles and responsibilities of all parties concerned so as to avoid conflicts. In doing so, chains of command and lines of communication should be defined, as well as the means by which necessary information should be obtained and transferred through these structures.
As part of the onsite emergency plan, individuals should be nominated for the following roles, among others:
Onsite (enterprise) co-ordinators to take control of the scene in the event of an emergency.
Onsite main controllers from the emergency control centre of the enterprise to take overall control of an emergency and to communicate with public authorities.
A person responsible for initiating activation of the offsite plan.
A person responsible to assist response personnel with information, expertise and other resources, as needed.
In establishing the responsibilities for various employees in the event of an accident, the onsite emergency plan should be flexible so as to manage foreseeable variations in staffing, taking account of such matters as absences due to sickness, holidays and periods of installation shutdown.
The role of the onsite co-ordinator and site main controller in relation to external emergency response personnel should be clearly defined to avoid any potential conflicts. The onsite co‑ordinator and controller may be subject to decisions made by the accident (on-scene) co‑ordinator of the public authorities. The onsite co‑ordinator and controller need to co‑ordinate with the accident co‑ordinator of the public authorities. Mechanisms and protocols should be established within the emergency plan to facilitate this.
The preparation and implementation of the onsite emergency plan should be the responsibility of management in co-operation with other employees.
All employees, including sub-contractors, at a hazardous installation should be made fully aware of the relevant provisions of the onsite emergency plan. In particular, they should be made aware of what to do in the event of an emergency, such as taking action to limit the release of hazardous substances and/or evacuating the installation and gathering at a previously designated assembly point.
All employees should be informed of the procedures for raising the alarm in the event of an accident or threat of an accident to ensure that the earliest possible action is taken.
Onsite managers should ensure that appropriate employees are familiar with the capabilities and emergency response plans of the fire authorities and other emergency responders.
Visitors to a hazardous installation should be provided with relevant information concerning what they should do in the event of an emergency and they should generally be accompanied at all times by a facility employee.
Management of hazardous installations should ensure that sufficient quantities of appropriate emergency supplies are available. Management should be aware which supplies have a limited shelf life. It may be appropriate to develop plans on how to obtain supplies at very short notice, e.g. specialist firefighting foam and absorbent material.
Any hazardous installation that does not have all of the necessary knowledge and expertise to undertake emergency planning should seek assistance to meet this obligation. This could be from trade associations, consultants, neighbouring installations, suppliers or public authorities.
Facilities in the same geographic area (including, for example, facilities within port areas or facilities in an industrial park) should co-ordinate their onsite plans and response activities in order to ensure the plans are consistent, establish systems for mutual aid when needed and help avoid domino effects.
The onsite plans should be available for review by public authorities and provided to the appropriate public authorities for the development and co‑ordination of offsite emergency plans.
Co‑operate with the development of offsite emergency plans
Management should work with public authorities in the development of offsite plans to ensure that the people responsible for the preparation of offsite plans have all the necessary information for their plans, including information needed to assess hazards and to help ensure the compatibility of offsite and onsite plans.
As part of the emergency planning process, management should co-operate with emergency responders to consider response options to various accident scenarios and to agree on appropriate options for different scenarios.
For emergency preparedness, response and follow-up purposes, management should make available health-related information concerning the hazardous substance(s) it manufactures and/or distributes, stores, handles, processes, disposes of or otherwise uses in the workplace. This includes information on the composition and toxicological, eco-toxicological and other relevant properties of hazardous substances, including solvents and additives.
In addition to information concerning the installation and the chemicals onsite, management should co‑operate with public authorities in the routing and identification of pipelines and transport routes outside the boundary fence of the hazardous installation that carry hazardous substances to and from the installation.
Management should never withhold information needed for the development of emergency plans. Thus, the claim that information is a trade secret or confidential business information should not be used as an excuse to withhold this information. However, arrangements should ensure that anyone who receives sensitive information maintains its confidentiality and security, as appropriate.
Industry should co-operate with public authorities to ensure that the potentially affected public has the appropriate information to understand potential chemical accidents which may occur and the appropriate actions to be taken in the event of an accident. Management and other employees at hazardous installations should maintain close relations with community leaders, education facilities and other members of their local population in order to help promote awareness and understanding of chemical accident risks.