This chapter focuses on the sourcing phase of the life-cycle and provides considerations for sustainable design from a chemicals perspective that are most relevant for this phase. Examples of trade-offs that arise in the sourcing phase are presented.
A Chemicals Perspective on Designing with Sustainable Plastics
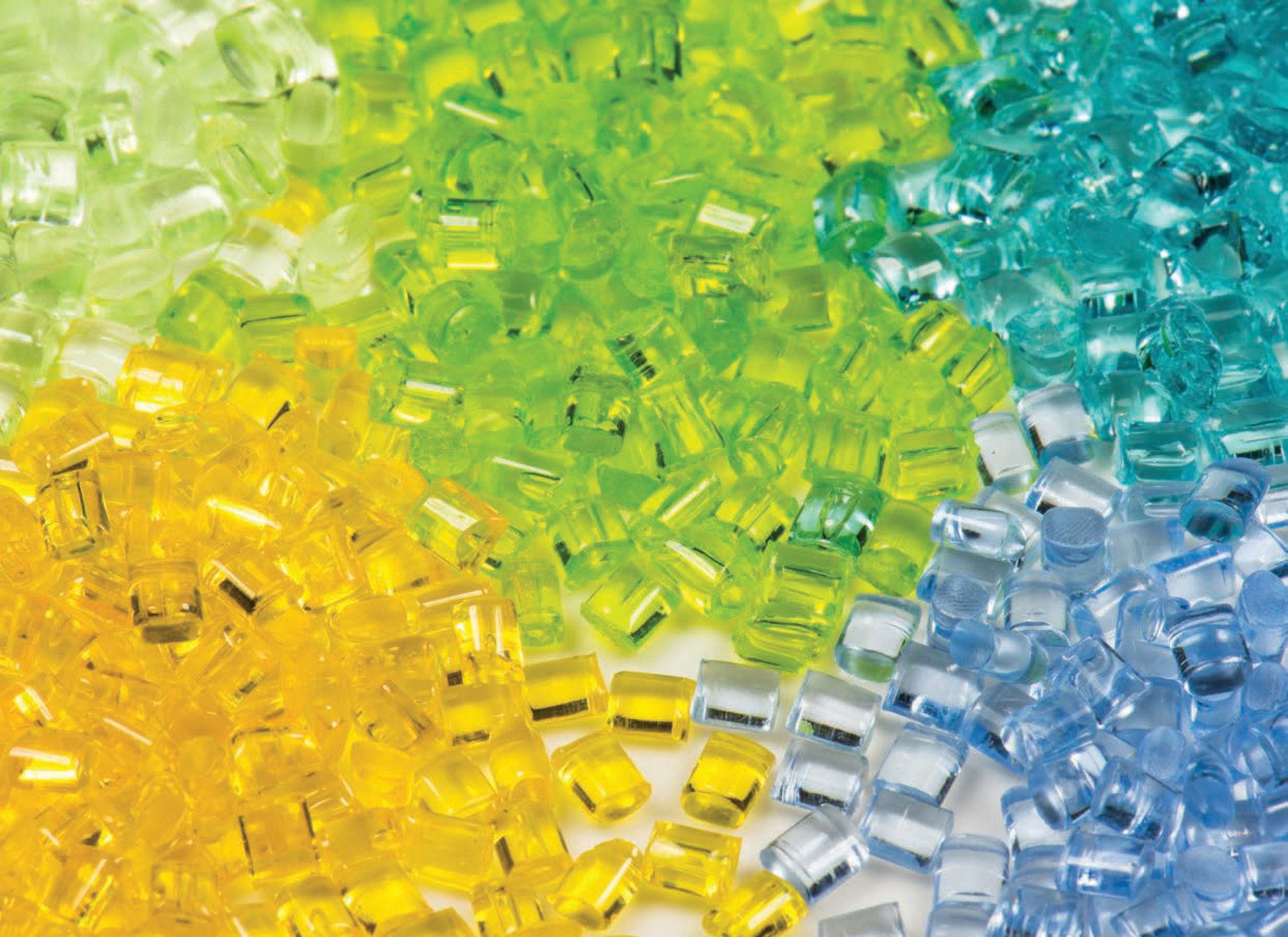
Chapter 4. Considerations During the Sourcing Phase
Abstract
In the sourcing phase of the life cycle, the plastic pellets that will be used to make the product part are produced. Source materials include the primary chemicals and intermediates used to produce monomer(s) and catalysts/reagents/process chemicals. The sourcing phase includes the extraction of the feedstock and the production of the polymer. The sourcing considerations relevant for all types of products are as follows:
A. Select a base polymer (secondary or primary renewable source; secondary or primary non-renewable source) that:
has the least emissions during extraction and production.
uses non-hazardous or the least hazardous chemicals during extraction and production.
minimises worker exposure during extraction and production.
B. Primary renewable feedstock (i.e., bio(based)plastics) is potentially a sustainable source, when:
the benefits of using this feedstock, demonstrated through life-cycle assessment, outweigh the costs of externalities, such as water consumption, and competition with food production or social or ecological land use.
the availability and continuity of availability of the supply of the feedstock enables its use.
C. Secondary feedstock is potentially a sustainable source, when:
the propagation of hazardous chemicals is avoided.
the resulting material contains a high percentage of the recycled material when designed.
the current and future availability of the supply of the secondary feedstock enables its use.
D. Primary non-renewable feedstock can be used as last resort, if it minimises hazardous chemicals or hazardous mixtures of chemicals.
E. Strive for transparency in chemical compositions throughout the value chain.
Some of the above considerations, like emissions, are also relevant (and discussed) in the other lifecycle phases and should be considered holistically. A material that has lower emissions during extraction and production may end up having greater emissions at end-of-life or even across the whole life cycle. Feedstock selection should be informed by the benefits of matching the waste management operations in the intended market. If a material is bio-based and biodegradable for example, biodegradation/composting is a suitable choice, if the appropriate infrastructure is in place and if the material does not contain hazardous chemicals or hazardous chemical mixtures.
4.1. Considerations During the Sourcing Phase
In the following section, the considerations for the sourcing phase are further explained. Note that the considerations under A apply to the selection of all different sources: primary renewable feedstock (paragraph B), secondary feedstock (paragraph C) and primary non-renewable feedstock (paragraph D).
A. Select a base polymer (secondary or primary renewable source; secondary or primary non-renewable source) that:
has the least emissions during extraction and production.
The extraction of the base polymer/source material and production of the polymer generate various emissions. “Waste” streams throughout this phase of the life cycle should be kept in the loop and at least recycled into another material. Emissions that cannot be kept in the loop should be specified (e.g. carbon dioxide (CO2), methane and emissions harmful to human health and the environment). Tools to assess emissions during lifecycle phases are described in Annex A: Overview of Relevant Methods, Tools and Metrics.
uses non-hazardous or the least hazardous chemicals during extraction and production.
Understanding the potential hazard(s) of chemicals in plastic types and possible exposure to these hazards enables design teams to select the most sustainable material options.
Hazards can emerge from the input chemicals and the production process (e.g. production residues, reaction products and other non-intentionally added substances).
Box 4.1. What can the design team do to prevent or minimise the use of hazardous chemicals at the sourcing phase
Discuss potential hazards (i.e., primary chemicals, intermediates, monomers, and catalysts) with the supplier/producer.
Tip: Note that there can be significant differences between production facilities for the same base polymer material. A series of Chemical Hazard Assessment methods and tools is provided in Annex A.
If hazardous source material is inevitable:
Prioritise suppliers that use a closed system to avoid exposure and disclose the use and release of chemicals of concern and express the desire for green chemistry solutions.
Re-evaluate the shortlist of polymers by asking if innovation is required on a material level.
Tip: Tools for the substitution of safer chemicals are available (e.g. European Chemicals Agency or ECHA).
Zoom out and re-evaluate the product design to consider whether another form of part/product could be chosen.
minimises worker exposure during extraction and production.
During the sourcing phase, extraction and production workers can be exposed to hazardous chemicals. Exposure depends on a variety of factors such as physical and chemical properties, its volume and production conditions.
B. Primary renewable feedstock (i.e., bio(based)plastics) is potentially a sustainable source, when:
the benefits of using this feedstock, demonstrated through life-cycle assessment, outweigh the costs of externalities, such as water consumption, and competition with food production or social or ecological land use.
The chosen polymer(s) for the product part has one of three sources: primary renewable feedstock, secondary or recycled feedstock (paragraph C) or primary non-renewable feedstock (paragraph D).
A resource is considered renewable when the regeneration is able to keep up with the extraction and consumption of the material. Rapidly renewable resources are selected to decouple feedstock extraction from fossil resources and reduce the emission of greenhouse gasses. The feedstock is not considered sustainable when it requires the destruction of natural capital (e.g. deforestation of rainforests to gain arable land). The cultivation of crops for plastic production should also not compete with pharmaceutical or food production in areas where arable land or water is scarce, or crop yields are unstable. By-products or residues of food production can be selected as feedstock in these cases.
Furthermore, if the cultivation of the feedstock heavily depends on fossil-based energy, through petrol for tractors or on the use of fertilizers, use of hazardous substances such as pesticides, or large amounts of fresh water, the overall environmental impact of the feedstock might be higher than that of fossil-based alternatives. Therefore, renewable feedstocks should always be evaluated for their full Life Cycle Assessment (LCA) and economic and social impact. Credible third-party certification can provide a direction to the design team in the selection of sustainable renewable feedstock. See Annex A: Overview of Relevant Methods, Tools and Metrics.
the current and future availability of the supply of feedstock enables its use.
A certain continuity of the sourcing of the feedstock is needed to invest in research and development throughout the supply chain. An extra difficulty for renewable feedstock is the need to deal with more extreme seasonal differences, so risk spreading or the use of a combination of several sources is an important factor to take into account.
C. Secondary feedstock is potentially a sustainable source, when:
The use of secondary feedstock, or recycled plastics, generally decreases the environmental and health impact of material production, prevents waste, and incentivises collection and recycling of the plastic at end-of-use.
the propagation of hazardous chemicals is avoided.
Be mindful of possible hazardous chemicals coming from production residues (e.g. monomers, oligomers and catalysts), additives (e.g. impact modifiers and pigments), non-intentionally added substances (e.g. side products or degradation products) and legacy chemicals from previous uses (e.g. residual inks and adhesives in secondary feedstock). Choosing mechanically recycled plastics can be challenging as information on their chemical content is often unavailable. In chemical recycling, there is the possibility to capture and remove the so-called "legacy" chemical additives and chemicals of concern that may be present in discarded plastics. However, chemical recycling is relatively immature and not a widespread option. Further, the energy instensity of available chemical recycling processes raises concerns for the environmental impacts and benefits of chemical recycling. In both cases, reliable material streams where the producer has considerable control over the process are preferred.
Suppliers should always be asked for material screening to identify hazardous chemicals and reasonably expected NIAS. The absence of hazardous chemicals in the feedstock should be ensured.
the resulting material contains a high percentage of the recycled material when designed.
The design team could aim for the highest percentage of recycled material possible when there are no legislative limits on percentages of recycled content. The use of recycled plastic in a new product increases the demand for recycled plastics, which in turn creates an incentive for collection and recycling at end-of-use.
A knowledge gap exists in current material databases. Virgin plastic grades are not the same as recycled grades. Find out which material can fulfil the design requirements, and then check with material experts whether the corresponding recycled material is suitable. Design from Recycling guidelines developed by PolyCE could be used to inform this (PolyCE, 2021). Also, check with manufacturing process experts as to how much recycled content can be used in a given application and on existing processing equipment.
the current and future availability of the supply of the secondary feedstock enables its use.
The availability of recycling infrastructure varies globally and, therefore, so does the availability of recycled feedstock. In addition, affordability impacts access especially when market prices for primary non-renewable feedstock are cheaper than secondary feedstock, which has sometimes been the case.
Note that the grade of the recycled content should match the ‘grade’ of the application of the plastic product. As food grade recycled plastic availability is limited, it should not be employed in applications that do not have a food grade requirement.
D. Primary non-renewable feedstock can be used as last resort, if:
Primary non-renewable feedstock, or “virgin plastic”, should only be used when renewable and secondary feedstock cannot be used. Its use is not sustainable as it requires the extraction of finite resources and inherently means that already extracted resources are not employed. The chosen primary non-renewable plastic should at least be readily reusable or recyclable (preferably retaining its quality, i.e., excluding downcycling), especially when the lifetime of the product is short.
it minimises hazardous chemicals or hazardous mixtures of chemicals.
If the use of virgin plastics is not completely avoidable/substitutable (e.g. as a combination is needed with recycled content to attain certain specifications), virgin resin may pose a toxicity risk to human health or biodiversity, just as recycled plastics. Hazardous chemicals could emerge from production residues (e.g. monomers, oligomers, catalysts), additives (e.g. flame retardants, heat and oxidation stabilisers, and pigments), and NIAS (e.g. due to degradation). Virgin plastics that minimise hazardous chemicals or hazardous mixtures of chemicals should be used.
Box 4.2. Example of sourcing phase considerations in the packaging sector
In food-contact applications such as biscuit packaging, the application of plastics from secondary feedstock is limited. Food safety regulations prohibit the use of plastics with risks of contamination in food-contact applications because contamination with hazardous chemicals is difficult to exclude. Processes exist to guide the certification of food contact grade plastics including those from recycled source materials. Consult the OECD case studies (OECD, 2021c; OECD, 2021d) for an evaluation of polymers from renewable feedstock (i.e., BioPE (polyethylene), BioPP (polypropylene), BioPET (polyethylene terephthalate), PLA (polylactic acid) and regenerated cellulose) and secondary feedstock (i.e., recycled LDPE (low density PE), recycled HDPE (high density PE), recycled PP, recycled PET, PA (polyamide), PLA, and regenerated cellulose) according to these considerations. These case studies outline considerations of certain polymers and additives for the design of packaging.
E. Strive for transparency in chemical compositions throughout the value chain.
To support (more) informed decision-making concerning the chemicals used in manufacturing, as much transparency as possible is important to identify what is known and where data gaps lie. Unfortunately, the composition of all materials is not typically fully known, nor are hazard data complete, but designers are trained to work with uncertainties. Relevant information on chemical composition (and its effect on health and the environment, i.e. hazard data) should also be passed along the value chain so that manufacturers, governments, users, consumers and recyclers have efficient access to information. Information on product composition should be kept available for at least the entire life span of the product, after products are marketed. Ideally, this information could be retained and auditable at each stage. Designers can consider material passports at chemical level. Blockchain with chemical markers, watermarks or QR codes are possible solutions.
4.2. Trade-Offs within the Sourcing Phase
Table 4.1. Various trade-offs emerging from taking sourcing phase considerations into account
Lowest emissions during extraction and production |
vs |
Use of secondary feedstock |
Secondary feedstock generally decreases the environmental impact of material production, but due to legacy chemicals they potentially could emit hazardous volatile organic compounds (VOCs) during production. |
||
Lowest (exposure to) hazardous chemicals during extraction and production |
vs |
Use of secondary feedstock |
Secondary feedstock generally decreases the environmental impact of material production, but there is a risk for legacy hazardous chemicals. Choosing recycled plastics can be challenging because information is often lacking on the chemicals in the plastics. Previous use cycles may have included toxic additives or other additives that are undesirable for the next use cycle. Information also is lacking on how well different plastics undergo multiple cycles. For Packaging Plastics this information is available (Schyns, 2021). |
||
Lowest emissions during extraction and production |
vs |
Lowest emissions during the whole life cycle |
Polymers with the least emissions during extraction and production may not necessarily deliver the greatest carbon abatement outcome over the whole life cycle. The alternative with the greatest carbon abatement outcome should be selected. |
||
Reduced material use |
vs |
Use of fewer material types |
A designer should consider the trade-off between use of an extra component (e.g. addition of a heat sealable layer to a film) and that of reduced material use (e.g. when using an oriented film). |
||
Reduced material use |
vs |
Close material loops |
Light weighting of products to reduce material use might require polymers of virgin quality. However, to effectively close material loops, recycled content in products should be maximised, possibly leading to heavier designs. Furthermore, certain polymers require less material in production (e.g. PET in bottles compared to HDPE bottles) but are sourced from a scarce stream (e.g. food grade recycled PET). |
||
Reduced material use |
vs |
Reduced virgin resin use |
Due to lower quality of recycled plastic, products may have increased thickness to meet product requirements, so they use more plastic, are heavier, but (should) have the advantage of using less virgin plastic. |
||
Cost of value chain |
vs |
Benefits of value chain |
Many virgin polymers come from long and established value chains, whereas new secondary or renewable feedstock come from shorter chains, where knowledge gaps emerge regarding hazards. Conversely, it could also be that an inexpensive polymer has a complex and long value chain, while a more expensive polymer has a clear short value chain with few hazards. |
References
OECD (2021c), “Case Study on Detergent Bottles; An example of weighing sustainability criteria for rigid plastic non-food packaging”, Series on Risk Management, No. 63, OECD, Paris.
OECD (2021d), “Case Study on Biscuit Wrappers; An example of weighing sustainability criteria for plastic flexible food packaging from a chemicals perspective”, Series on Risk Management, No. 64, OECD, Paris.
PolyCE (2021), Design for Recycling Design from Recycling - Practical guidelines for designers. Post-Consumer High-tech Recycled Polymers for a Circular Economy – European Commission Funded Project, ISBN 978-90-813418-0-6, https://www.polyce-project.eu/wp-content/uploads/2021/04/PolyCE-E-book-Circular-Design-Guidelines-2.pdf
Schyns, Z. O. G. and M. P. Shaver (2021), "Mechanical Recycling of Packaging Plastics: A Review." Macromolecular Rapid Communications, Vol. 42, No. 3, pp. 2000415.