This chapter focuses on the manufacturing phase of the life-cycle and provides considerations for sustainable design from a chemicals perspective that are most relevant for this phase. Examples of trade-offs that arise in the manufacturing phase are presented.
A Chemicals Perspective on Designing with Sustainable Plastics
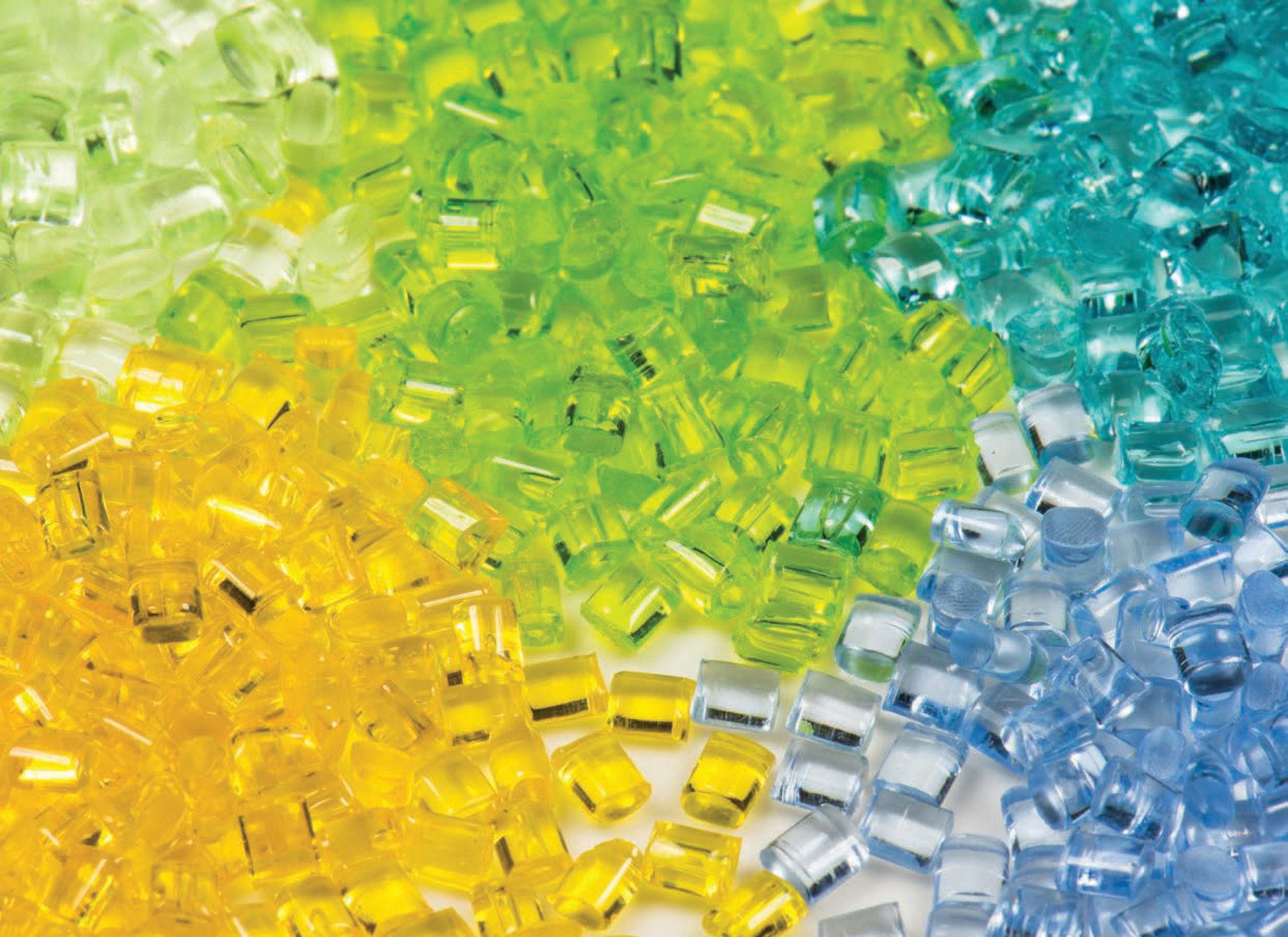
Chapter 5. Considerations During the Manufacturing Phase
Abstract
During the manufacturing phase of the life cycle, the plastic granulates are made into a product part. Common chemical types used in the process are raw materials, monomers, oligomers, catalysts, polymers, performance additives (e.g. anti-oxidants, colorants, plasticisers, UV stabilisers, flame retardants, compatibilisers, etc.), and manufacturing and processing aids (e.g. lubricants, anti-block and slipping agents, and antistatic agents). Several considerations need to be taken into account throughout the manufacturing phase:
A. Select a manufacturing technique that:
generates the least emissions.
uses the least processing aids.
uses non-hazardous or the least hazardous chemicals.
minimises worker exposure.
B. Consider sustainable manufacturing on a systems level.
C. Ensure transparency in chemical composition throughout the value chain.
5.1. Considerations during the Manufacturing Phase
In this section, the considerations for the manufacturing phase are further explained.
A. Select a manufacturing technique that:
generates the least emissions.
Manufacturing plastic products can generate various emissions. “Waste” streams throughout this phase of the life cycle should be kept in the loop and at least recycled into another material. Emissions that cannot be kept in the loop should be specified (e.g. CO2, methane, and emissions harmful to human health and the environment). Tools to assess emissions during lifecycle phases are described in Annex A: Overview of Relevant Methods, Tools and Metrics.
Consider the emissions calculated with life cycle analysis for diverse manufacturing techniques to compare them. Consult the OECD case study on detergent packaging to learn more about the sustainability of extrusion blow moulding compared to injection stretch blow moulding (OECD, 2021d).
uses the least processing aids.
Find a manufacturing technique that minimises the variety of types of chemicals and their quantity required to abate the consequent environmental pollution and human exposure. Moreover, consider the energy consumption (i.e., amount and source of energy), water consumption and overall waste produced to compare manufacturing techniques.
Questions to ask suppliers and producers: What chemicals are used as processing aids and in what quantity? Are the facilities tracking their emissions and their energy, water, and material use? Have they set goals to reduce these?
uses non-hazardous or the least hazardous chemicals.
Consideration of chemical hazards are key when designing sustainable plastic products. Chemicals needed during the manufacturing processes and that will be present in the finished plastic article should first be identified. Their hazards and particular properties (e.g. persistency or mobility in the environment, potential to bioaccumulate) should assessed. Use of chemicals that are, for example: carcinogenic, mutagenic, or toxic to reproduction (CMR), Persistent, Bioaccumulative and/or Toxic (PBT), very Persistent and very Bioaccumulative (vPvB), Persistent, Mobile, and Toxic (PMT) or are of other concern, such as Endocrine-Disrupting Chemicals (EDC) should be avoided.
The use scenarios for a product define the requirements for manufacturing techniques, as well as all the other life cycle phases. With products that come into close contact with food or skin (e.g. food packaging, toys) particular efforts are warranted, such as not using any hazardous substances.
Box 5.1. What can the design team do to prevent or minimise the use of hazardous chemicals at the manufacturing phase
Consider and compare manufacturing processes based on their possibility to minimise the use and release of hazardous chemicals and pollution.
Tips: Be aware that a chemical inventory is limited by current knowledge. Currently not all additives and non-intentionally added substances (NIAS) can be identified. Diverse assessment methods, each with their own data needs, can be applied (see Annex A). Also, do not only consider currently regulated substances, take future regulatory actions on emerging chemicals of concern into account when possible.
The OECD created the Substitution and Alternatives Assessment Tool Selector enabling designers to evaluate the most suitable hazard assessment tool.
Consider whether the function of that chemical is crucial for product performance and remove if possible.
If it cannot be removed, find alternatives for hazardous chemicals.
Tip: Check guidance (OECD, 2021; ECHA, n.d.)
If no alternatives to hazardous chemicals were found:
Seek a supply chain where the desire for environmentally conscious chemistry solutions was expressed.
Tips: Consider how stringent the legislation on hazardous chemicals is at the manufacturing location. Regulation that is more lenient will lead to more risks in the supply chain.
Questions to ask suppliers and manufacturers:
Are the facilities tracking the use of all chemicals (particularly hazardous chemicals) throughout the manufacturing process? This includes chemicals composing the product (both polymer and additives), as well as processing aids.
Are the facilities tracking the release of all chemicals (particularly hazardous chemicals), including compliance with waste regulations?
Are the facilities reporting this information along the value chain?
Have the facilities set goals for eliminating or reducing the use and release of hazardous chemicals?
Re-evaluate the shortlist of polymers: is innovation on a material level required?
Zoom out and re-evaluate the product design to consider whether another form of part/product could be chosen.
minimises worker exposure.
Consider what exposure scenarios are to be expected during the manufacturing processes studied.
Prioritise consideration of occupational and environmental exposures to hazardous chemicals, and toxic emissions and waste. Comparative exposure mapping helps to pinpoint potential exposure pathways. Qualitative exposure assessments can be based on the presence of chemicals in a form that can be inhaled, ingested or absorbed through the skin during the manufacturing of the product part.
Box 5.2. Example of a construction sector-specific consideration concerning exposure during manufacturing
Consider the risk of monomer exposure for closed cell rigid foam manufacturing, because the polymer is formed during this process. In contrast, polystyrene insulation is made from the polymer. Consult the OECD case study (OECD, 2021b) for an evaluation of manufacturing processes for four types of plastic insulation.
B. Consider sustainable manufacturing on a systems level
It is important to take into account the environmental impacts associated with the manufacture and distribution of products. For example, if a product consists of different parts that are to be mounted together, consider a physical design of parts to avoid the need of glue. By such design choices, additional chemicals can be avoided and the product will more easily be reused or recycled. For transport, consider the distance between the manufacturing facility where product parts are made and the location where they are assembled or completed (e.g. filling a bottle of detergent). Ideally, these processes occur at the same location, with limited distance to retailers. When this is not possible at the same location, another manufacturing technique could be considered. For instance, it is recommended to assess the environmental impact of transporting empty bottles to be filled versus reheating preforms for injection stretch blow moulding on location.
Question to suppliers or manufacturers: what measures are in place to track and report key sustainability measures?
C. Ensure transparency in chemical composition throughout the value chain.
To support informed decision-making concerning the chemicals used in manufacturing, transparency is important to identify what is known and where data gaps lie. A tiered and iterative approach to chemicals inventory could be used (i.e., “starting with higher disclosure thresholds, and working to gather additional information at lower thresholds as feasible and relevant”).
For example, the Global Automotive Declarable Substance List (GADSL) can be used to assess substances expected to be present in automotive products through the supply chain.
5.2. Trade-Offs within the Manufacturing Phase
Table 5.1. Various trade-offs emerging from taking manufacturing phase considerations into account
Benefits of efficient manufacture |
vs |
Consequences of the required additives on hazard, energy/water/material use |
Certain additives (like anti-static agents) can ease or speed up the manufacturing process, but consequently require more material use or create hazards. |
||
Known hazardous chemical |
vs |
Uncertain hazard of chemical |
Even if chemical contents are known, most chemicals do not currently have full hazard assessments, meaning data gaps exist in one or more hazard endpoints. A design team may have to choose between a chemical that is known to be hazardous and a chemical that is not known to be hazardous but has gaps in hazard data. |
||
Reduce material use |
vs |
Reduce hazards |
Certain plastics (like insulation materials) are very efficient in volume, mass or thickness, but contain more potential hazardous substances in compared with less efficient materials. While resource efficiency is important and frequently has direct economic implications (e.g. energy consumption), it is important that designers consider resource efficiency metrics separately from metrics that address exposure to human health or environmental hazards. They are linked to different sustainable design principles and should not be aggregated. |
||
Benefits of increased performance |
vs |
Consequences of the required additives on hazard, energy/water/material use |
Increased product complexity or additives included to improve performance should be considered in terms of the potential trade-offs for other life cycle stages. Innovative product design or additives, or complete reimagining of the materials that make up the product, can be used to maintain or increase performance without increasing hazards or introducing other environmental impacts. |
References
ECHA. (n.d.). Substances of concern: Why and how to substitute? European Chemicals Agency, Helsinki, Finland, https://echa.europa.eu/documents/10162/24152346/why_and_how_to_substitute_en.pdf/93e9c055-483c-743a-52cb-1d1201478bc1
OECD (2021), “Guidance on Key Considerations for the Identification and Selection of Safer Chemical Alternative”, Series on Risk Management, No.60, OECD, Paris, https://www.oecd.org/chemicalsafety/risk-management/guidance-on-key-considerations-for-the-identification-and-selection-of-safer-chemical-alternatives.pdf
OECD (2021b), “Case Study on Insulation: An example of chemical considerations for sustainable plastics design”, Series on Risk Management, No.66, OECD, Paris.
OECD (2021d), “Case Study on Biscuit Wrappers; An example of weighing sustainability criteria for plastic flexible food packaging from a chemicals perspective”, Series on Risk Management, No. 64, OECD, Paris.