This chapter brings together the considerations highlighted across the various life-cycle phases in order to consider whole product assessment and optimisation of the design. When doing so, trade-offs emerge between the life cycle phases and examples of these are presented.
A Chemicals Perspective on Designing with Sustainable Plastics
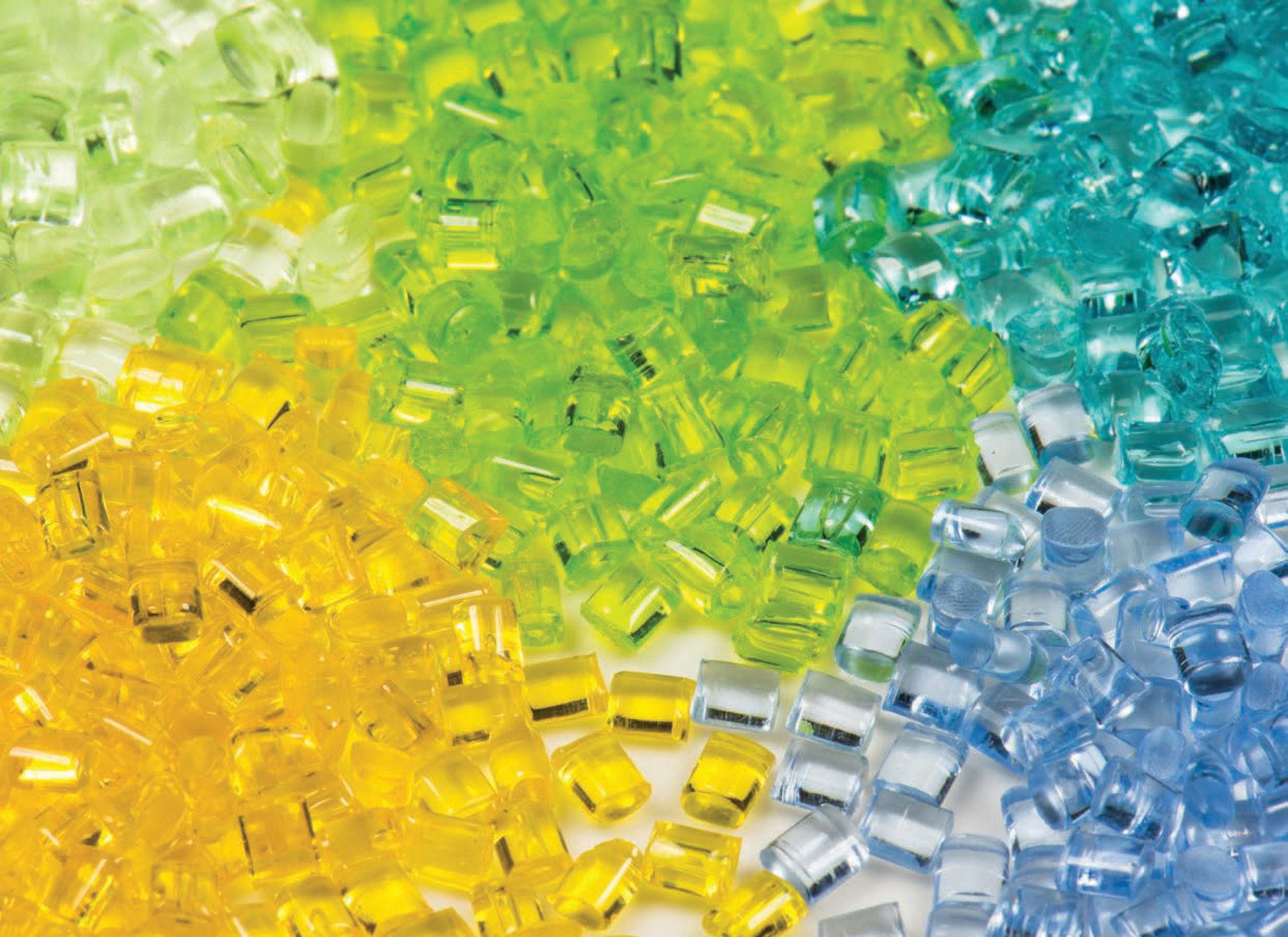
Chapter 8. Whole Product Assessment and Optimisation
Abstract
After looking at every phase of the life cycle separately, designers and engineers need to combine the considerations from every phase. When doing so, trade-offs emerge between the life cycle phases.
The material selection can be optimised for the sustainable design goals. The design team should look for dominance in options (i.e., win-win situations). This chapter identifies the resulting trade-offs and illustrates how to deal with them.
8.1. Trade-Offs between Life Cycle Phases
The decisions or constraints in one phase of the life cycle influence the possibilities in the other phases. Table 8.1 indicates how constraints set in the top row of the table influence the phases in the column on the left. The list is non-exhaustive and should be complemented by the design team.
Table 8.1. Dependencies between decisions and constraints in one life cycle phase to the other phases
How Influences |
Sourcing |
Manufacturing |
Use |
End-of-Use |
---|---|---|---|---|
Sourcing |
- A selected production method requires specific feedstock. - A selected production method requires the use of specific additives. |
- Non-negotiable design requirements (e.g. function of the product, food safety, barrier properties and chemical resistance) limit sourcing options. |
- Aiming for product-to-product recycling limits the polymer and sourcing options. - A preferred end-of-use scenario limits the number of possible materials. - Recycled content vs recyclability. |
|
Manufacturing |
- Available polymers might require specific production methods and additives. |
- Non-negotiable design requirements (e.g. function of the product) can lead to production residues to which installers are exposed. These could have been avoided at the production phase if the requirement was negotiable. - Non-negotiable design requirements (e.g. barrier properties) may require bonding of multiple materials. |
- Sorting and mechanical recycling depends on the product design. - Recycling or composting preference limits the material options during manufacturing. |
|
Use |
- Properties of the available materials might not meet design requirements. - Some plastics emit hazardous volatile organic compounds (VOCs) during their sourcing process, but current alternatives without hazardous VOCs could have a much shorter lifespan. |
- Usability of the product. - The production method requires additives that might migrate (e.g. to the food). - Some plastics emit hazardous VOCs during their sourcing, but current alternatives without hazardous VOCs could have a much shorter lifespan. - To use fewer materials in the product itself, additional products will be needed to support use (e.g. potentially hazardous adhesives to install the product). |
- Preferred end-of-use scenario limits the use of combined materials with optimal properties. |
|
End-of-Use |
- Selected polymers and their required additives might limit the end-of-use options. |
- Optimising manufacturing processes may reduce end-of-use options. |
- Non-negotiable design requirements (e.g. barrier properties, installation or function of the product) lead to materials/ contaminations during the use phase with low(er) recycling potential. |
Note that data gaps are encountered at every phase of the life cycle. One of these data gaps is the lack of (comparable) emissions data throughout the supply chain. Design teams should not neglect data gaps and should not assume there are no sustainability implications. They should strive to fill these in wherever possible, especially for life cycle phases where damage to human health and ecosystems is to be expected based on available benchmarks. The teams should explicitly keep track of unknowns along the way. When an appropriate disclosure is missing, a sensitivity analysis (to see how important an environmental release might be), exposure testing or substitution for safer chemicals is advised.
There can also be significant variation in emissions between manufacturing facilities for the same base polymer material. The theoretical embodiment of the product concept should be put to the test with practical knowledge from specific suppliers who will provide the material and relevant circular processors who will most likely treat the products at their end-of-use. The sustainable design goals, life cycle considerations and trade-offs help guide the discussions with these stakeholders.
8.2. Dealing with Trade-Offs
In the case of trade-offs, designers and engineers will have to carefully evaluate considerations to favour one over the other. This process is guided by the ranking of the sustainable design goals and the non-negotiable conditions defined in Chapter 3. Transparency throughout this process is important to support credibility and ensure that decisions are traceable.
To illustrate how to deal with trade-offs, the example in Chapter 3, where closing resource loops is prioritised over slowing and narrowing resource loops for prioritising design goals (see Figure 3.1), is used to examine three trade-offs in the case of detergent bottles (Figure 8.1). The ranking example was as follows: 1. Select materials with inherently low risk/hazard; 2a. Use secondary feedstock or biobased feedstock, 2b. Have a commercial ‘afterlife’ (recycling); 3. Generate no waste; 4. Have a commercial ‘afterlife’ (other aspects).
The underlined terms in Figure 8.1 are decisive in the reasoning. The circled trade-offs are the ones that have been prioritised based on the reasoning in the right column. This approach can also be adopted to deal with the trade-offs emerging within the life cycle phases.
Figure 8.1. Example of trade-offs (two left columns) and how to deal with them (right column)
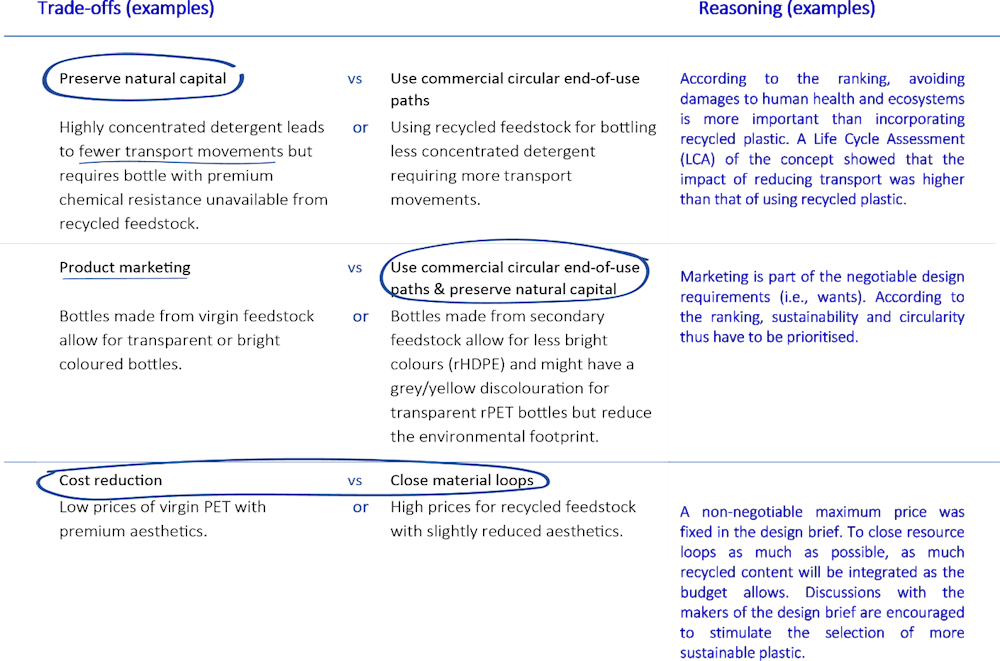